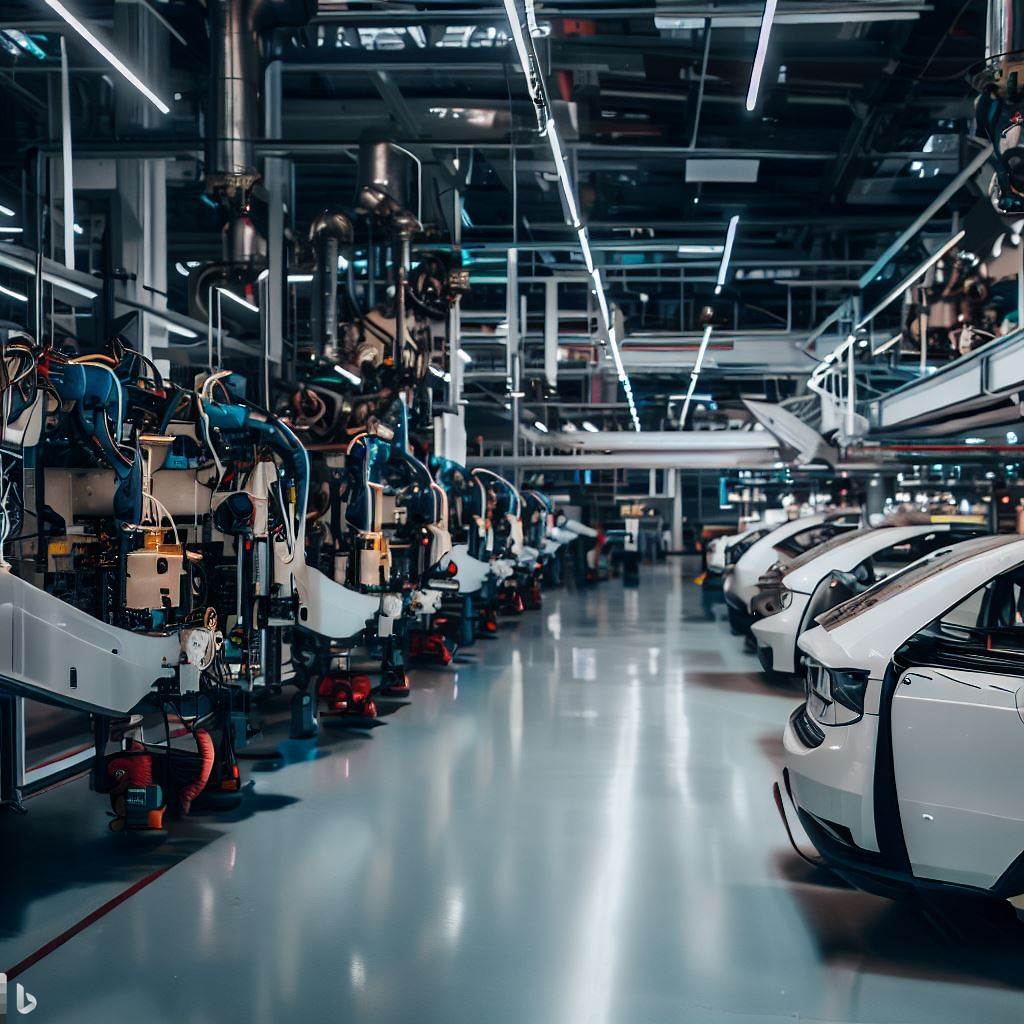
Disclaimer: I do not have any relation with Tesla. To write this post, I used publicly available information shared by Tesla (mainly from the 2023 Investor Day). This is my personal interpretation of those materials.
Tesla 2023 Investor Day
Recently I watched the Tesla 2023 Investor Day video on YouTube. It was a very interesting presentation on the world-class Industrial Internet of Things deployment.
I noticed many insights that I would like to share with you. Today, I will focus on automated testing in Industrial IoT.
Automated testing in Industrial IoT
Automated testing happens at every stage of an assembly.
Every component installed inside a car:
- registers itself,
- performs internal checks,
- tests cooperation with other subsystems.
A car is a complex ecosystem of multiple connected devices (sensors, actuators, processing units, etc.). Testing every change introduced to this system enables immediate detection of potential issues. That is a common approach during agile software development, but I rarely find it in Industrial IoT engagements.
Fixing connected hardware issues is trickier than solving software bugs. To find the root cause, we need to check both hardware and firmware of the installed part. Sometimes installed component works fine but reports an issue. In that case, another malfunctioning part might cause that problem.
Those kinds of bugs are hard to find and fix without automated testing and real-time status reporting from every subsystem.
The real-time reporting provides telemetry data not only to the shop floor IT but also to the backend system.
The backend system has greater visibility into the assembly line and gathers data from external/internal IT systems. That enables the backend to predict failures not recognized by the monitored subcomponent.
The identified issue is immediately fixed, with minimal impact on the production timeline. In the classical approach, (manual) testing happens at the end of the production stage. Fixing an identified problem might require dismounting several parts, which is time-consuming and error-prone.
Key takeaways:
- Gathering real-time telemetry data from the assembly line enables automated testing and prediction of issues.
- Automated testing improves the quality of manufactured units and production efficiency.
- Every component should be responsible for testing itself and its dependencies.
I hope those insights were interesting to you. I will share my additional observations in future posts.
